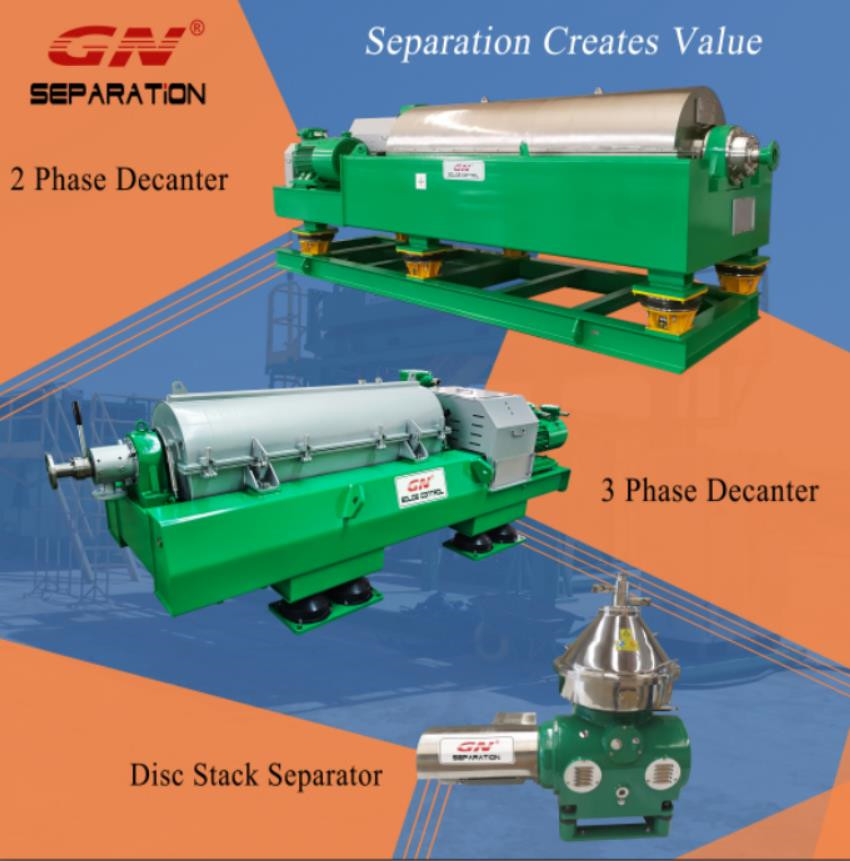
GN Separation is pleased to announce our participation in IFAT Eurasia 2025, the leading trade fair for environmental technologies in the Eurasian region. The event is scheduled to take place from May 15th to 17th, 2025 at the Istanbul Expo Center, and GN will be exhibiting at Hall 11, Booth No. 105E.
- Details
-
Published: 13 May 2025
In the upcoming week, GN Separation is gearing up to take part in the much - awaited IFAT Eurasia 2025, the foremost international event for environmental technologies in the region. This significant gathering is slated to occur from May 15th to 17th at the Istanbul Expo Center, and it has firmly cemented its position as the premier business platform for environmental technologies within the Eurasian market.
A Glimpse into IFAT Eurasia
Organized by Messe München and EKO MMI Fuarcılık Ltd. Şti., IFAT Eurasia acts as a crucial nexus for the environmental technology sector. It serves as a bridge, bringing together exhibitors and visitors from all corners of the globe. With its strong market influence and unwavering dedication to promoting innovation, IFAT Eurasia has become the ultimate destination for professionals in search of state - of - the - art solutions to tackle environmental issues.
GN Separation: A Pioneer in Environmental Solutions
GN Separation will be stationed at Hall 11, Booth 105E, eager to display its diverse array of products tailored specifically for the environmental field. Among its flagship offerings are Dewatering Centrifuges, Sludge Screw Presses, and Oily Sludge Treatment Systems, all meticulously engineered to provide dependable performance and high efficiency in waste management and resource recovery.
Dewatering Centrifuge
GN Separation's Dewatering Centrifuges are designed to excel in separating solids from liquids across a broad spectrum of applications. These include municipal and industrial wastewater treatment, sludge dewatering, and drilling mud management. Thanks to their sturdy build and advanced control systems, they guarantee reliable operation even under the most challenging conditions. As a result, they are the top choice for operators in pursuit of efficient and cost - effective dewatering solutions.
Sludge Screw Press
The Sludge Screw Press from GN Separation is another outstanding product, offering a highly versatile and efficient solution for sludge dewatering. It operates based on the principle of continuous filtration and compression. A rotating screw is used to transport sludge through a filter screen while applying pressure to squeeze out water. This makes it an ideal fit for small to medium - sized wastewater treatment plants, as it boasts a compact design, low energy consumption, and minimal maintenance needs.
Oily Sludge Treatment System
In response to the escalating demand for effective oily sludge treatment, GN Separation has developed its Oily Sludge Treatment System. This comprehensive and eco - friendly approach to managing oily waste integrates physical, chemical, and thermal treatment processes. It successfully separates oil, water, and solids from oily sludge, allowing for the recovery of valuable resources and a significant reduction in environmental impact.
Final Thoughts
As GN Separation gets ready to showcase its offerings at IFAT Eurasia 2025, the company is enthusiastic about connecting with industry experts, sharing its in - depth knowledge, and presenting its environmental solutions. We cordially invite you to visit GN Separation at Hall 11, Booth 105E, to discover more about its products and how they can enhance your operations.
- Details
-
Published: 09 May 2025
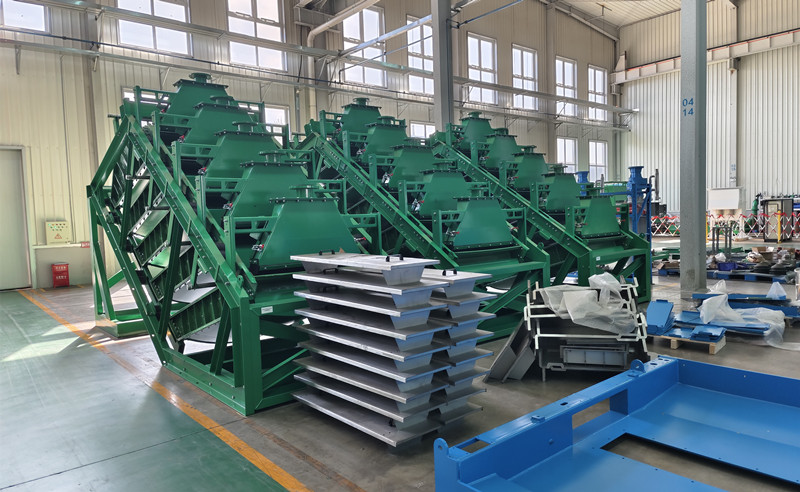
GN Separation is pleased to announce the successful completion and preparation of 8 sets of Stack Vibrating Screens (Fine Sizer models) for shipment to a valued domestic client. This batch marks another milestone in GN's continued commitment to delivering reliable and efficient fine screening solutions for industrial applications.
- Details
-
Published: 30 April 2025
This week, GN Separation achieved a significant milestone by successfully concluding the factory testing of eight high-frequency Stack Vibrating Screens. These screens are specifically designed for a domestic mining customer, marking another successful collaboration in the mining sector.
The Pivotal Role of Stack Vibrating Screens in the Mining Industry
In the mining industry, the effective separation and classification of minerals are paramount for streamlining production processes and optimizing the utilization of natural resources. GN's Stack Vibrating Screen has emerged as a cornerstone in this field, particularly for wet screening, classification, and dehydration of fine-grained materials. Its versatility in handling a wide spectrum of minerals, ranging from coal to various ores, makes it an invaluable asset for mining operations of all scales, from large enterprises to small and medium-sized enterprises.
The design of GN's Stack Vibrating Screen is characterized by its flexibility, allowing for configurations of 2 to 5 layers based on on-site requirements. This adaptability ensures seamless integration into existing processing lines, thereby enhancing the overall efficiency and productivity of mining operations. By precisely separating minerals according to size and quality, the Stack Vibrating Screen plays a crucial role in minimizing waste, improving recovery rates, and ultimately increasing the profitability of mining projects.
Key Features of GN's Stack Vibrating Screen
Advanced Vibration Technology
The screen is propelled by a dual vibration motor that operates on the principle of two-degree-of-freedom resonance, generating linear vibration throughout the machine. This cutting-edge vibration technology guarantees efficient screening and classification of materials, even at high frequencies, ensuring optimal performance.
High Screening Efficiency and Large Processing Capacity
Thanks to its unique vibration mode and optimized screen box assembly, GN's Stack Vibrating Screen offers high screening efficiency and a large processing capacity. This enables faster processing times and increased throughput, making it an ideal choice for high-volume mining operations.
Energy-Saving and Cost-Effective
The screen's design is engineered to minimize power consumption, thereby reducing operational costs. The use of high-quality materials and advanced manufacturing techniques ensures a long lifespan and low maintenance requirements, further enhancing its cost-effectiveness and return on investment.
Durable and Reliable Polyurethane Screen Mesh
The screen is equipped with a Polyurethane Screen Mesh, which boasts a high opening rate (28-45%) and an average lifespan of over six months. This material is highly resilient, resistant to clogging, and provides excellent wear resistance, ensuring consistent performance over an extended period.
Advanced Material Handling Features
The feeding box features a unit-combination structure with multi-level buffer steel plates and a material distribution plate. This design slows down the flow of materials, protecting the screen from excessive wear and tear. As a result, it extends the life of both the feeding box and the screen, reducing production and maintenance costs.
Corrosion and Wear Resistance
The surface treatment of the vibrating screen employs a sandblasting process and heavy anti-corrosion paint, providing exceptional corrosion resistance. The contact surface with the material is sprayed with polyurea resin, further enhancing wear resistance and prolonging the screen's lifespan, even in harsh mining environments.
These screens are now poised for deployment at domestic mining sites, where they will play a pivotal role in enhancing the efficiency and productivity of mineral processing operations. For more information on vibrating screens for mining applications, please do not hesitate to contact GN Separation.
- Details
-
Published: 30 April 2025
At the recently concluded IE EXPO CHINA 2025, GN Separation garnered significant attention, successfully forging new business collaborations and facilitating in-depth technological exchanges with both familiar and new industry contacts. The event served as an ideal platform for GN Separation to highlight its cutting-edge equipment designed specifically for environmental water treatment and solid waste management.
During the exhibition, GN Separation showcased three flagship products: the Solids Vacuum Pump, the Fully Hydraulic Decanter Centrifuge, and the 3 Phase Decanter Centrifuge. Each of these devices was engineered to tackle pivotal challenges in environmental engineering, spanning municipal sludge dewatering to intricate oil-water-solid separations.
Solids Vacuum Pump: A Multi-Faceted Solution for Material Handling
The fully pneumatic Solids Vacuum Pump stood out as a groundbreaking innovation, renowned for its reliable and efficient handling of a wide array of materials. Its applications extend across municipal and industrial sectors, encompassing:
- Sewage Sludge Removal: Ideal for clearing sedimentation tanks in wastewater treatment facilities.
- Construction Slurry Transport: Efficiently managing heavy mud from construction sites.
- Solid Waste Disposal: Capable of conveying granular solids such as sand and powdered residues.
Designed for durability, the pump operates without any electrical components, ensuring safety in potentially explosive environments and reducing long-term maintenance expenses. Its ability to adapt to varying material densities and particle sizes renders it a versatile solution for dynamic waste streams.
Fully Hydraulic Decanter Centrifuge: A Customized Dewatering Solution
The Fully Hydraulic Decanter Centrifuge by GN Separation distinguishes itself from conventional electric dewatering centrifuges by dynamically adjusting torque based on the characteristics of the feed material, thereby optimizing performance across a range of solid contents. Its key advantages include:
- Adaptive Torque Control: Ensures consistent cake dryness across diverse sludge types.
- Maintenance-Free Hydraulic Gearbox: Eliminates the need for routine servicing, thus lowering operational costs over time.
- Explosion-Proof Design: Certified for use in hazardous environments, including oilfields and chemical plants.
These features position it as a top choice for municipalities and industries seeking reliable and cost-effective dewatering solutions.
3 Phase Decanter Centrifuge: Precision Separation for Complex Waste Streams
The 3 Phase Decanter Centrifuge addresses the escalating demand for advanced separation technologies in environmental applications. Engineered to separate light liquid, heavy liquid, and solid phases simultaneously, it excels in:
- Kitchen Waste Oil Recovery: Extracting edible oils from food processing byproducts.
- Oil-Water Separation: Enhancing the efficiency of wastewater treatment in industrial settings.
- Oily Sludge Treatment: Recovering oil from contaminated sludge in refineries and petrochemical facilities.
By minimizing waste volume and recovering valuable resources, this centrifuge supports the principles of a circular economy while ensuring compliance with stringent environmental regulations.
Strategic Collaborations: Forging Alliances with Industry Pioneers
Beyond product demonstrations, GN Separation’s team engaged in comprehensive discussions with visitors, exploring potential partnerships in emerging markets and research endeavors. The company’s dedication to innovation was further emphasized through collaborations with universities and R&D institutions, focusing on the development of sustainable separation technologies.
- Details
-
Published: 25 April 2025
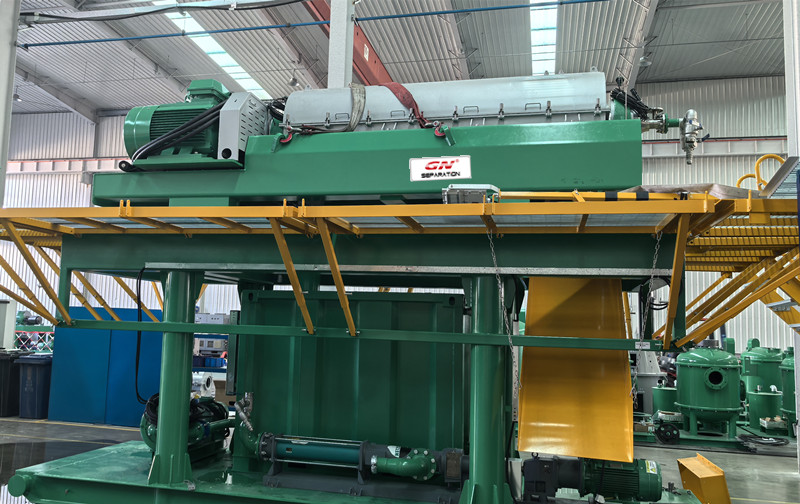
GN Separation is proud to announce the successful shipment of one of our large model dewatering decanter centrifuges, the GNLW654-VFD, to an overseas client for industrial sludge treatment. This delivery highlights the increasing global demand for GN's high-performance separation equipment and showcases our technical expertise in providing efficient, reliable, and energy-saving solid-liquid separation solutions.
Powerful Performance for Demanding Applications
The GNLW654-VFD is part of GN’s T Series dewatering decanter centrifuges, engineered with an optimized beach angle of 8.5 degrees to enhance dewatering efficiency and discharge drier solids. This model is specifically designed to handle materials with large particle size, high solid-liquid density difference, high concentration, and low viscosity, making it ideal for municipal and industrial wastewater, oily sludge, drilling mud, chemical wastewater, sand washing water, and more.
Key Features of the GNLW654-VFD
-
Large Bowl Design: With a 650 mm (25.6 inch) bowl diameter and 2730 mm (107.5 inch) length, the GNLW654 offers high throughput capacity and effective sludge dewatering performance.
-
High G-Force: Operating at a max speed of 2873 RPM, this model generates a G-force up to 3000G, facilitating rapid and thorough separation.
-
Premium Materials: The bowl and screw are made of duplex stainless steel (SUS2304 or SUS2205) through centrifugal casting, offering superior corrosion and wear resistance compared to conventional SS304 or SS316.
-
Energy-Efficient & Low Noise: The design includes a deep liquid pool, optimized cone angle, and anti-turbulence structures, contributing to better clarity, reduced energy consumption, and quieter operation.
-
Wear Protection: The solids discharge ports and screw flights are protected with tungsten carbide sleeves and replaceable wear-resistant tiles, ensuring long service life even under harsh working conditions.
-
Smart Control: Equipped with a VFD+PLC+HMI control panel, the centrifuge allows real-time monitoring of vibration, temperature, torque, and lubrication status. Emergency protocols such as automatic plugging and shutdown procedures are in place for safe operation.
-
Space-Saving Layout: Both motors are installed at one end of the unit for compact design and easier maintenance access.
Reliable Dewatering for a Wide Range of Materials
GN’s T Series decanter centrifuges are versatile and widely applied in industries such as:
-
Municipal wastewater and sludge treatment
-
Oilfield drilling fluids and oily sludge recovery
-
Sand and mineral washing
-
Steel-making and precision casting wastewater
-
River and lake dredging
-
Chemical, pharmaceutical, and food industry wastewater
-
Salt and kaolin recovery
-
Biomass, aquaculture, and more
For materials with fine particles, GN also recommends using flocculants to enhance solid aggregation before centrifugation, enabling more efficient separation.
Customized & Turnkey Solutions
In addition to standalone centrifuges, GN Separation offers complete dewatering process solutions by integrating our wide range of separation and conveying equipment. We support system customization based on project-specific requirements and deliver comprehensive support from equipment selection to on-site service.
About GN Separation
As a trusted manufacturer and exporter of separation equipment, GN Separation has supplied decanter centrifuges and related systems to over 80 countries worldwide. We take pride in offering reliable technology, premium materials, and responsive support to help our clients succeed in their environmental and industrial challenges.
GN Separation looks forward to working with you on your next dewatering or solid-liquid separation project. For more information about the GNLW654-VFD or other models in our T Series, feel free to contact us today.
- Details
-
Published: 20 April 2025